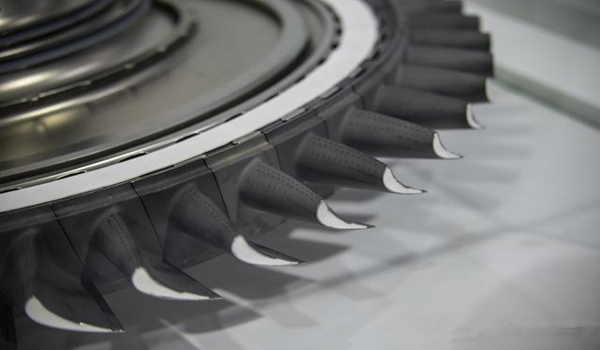
發(fā)動機展臺上的高壓渦輪盤
前不久,中航發(fā)動機展臺上有這么一件展品,這個展品是一個高壓渦輪盤,高壓渦輪盤的最外圈是一排渦輪葉片,在渦輪葉片上我們能看到很多排細小的氣孔。渦輪葉片的工作環(huán)境很惡劣,要承受很大的離心力,為什么還要在渦輪葉片上打孔呢?
這個還要從渦輪葉片的工作環(huán)境說起。以美國F22戰(zhàn)斗機配套的F119發(fā)動機為例,其渦輪前進氣溫度為1973K,換算為攝氏度就是1700℃。而F119發(fā)動機渦輪葉片用的是第二代單晶高溫合金CMSX-4,其工作溫度1040℃,熔點是1343℃。換句話說,發(fā)動機燃燒室產(chǎn)生的燃氣溫度比單晶高溫合金的熔點還要高出近四百度,那么燃氣吹在渦輪葉片上,它不會被融化嗎?渦輪葉片當然不能被融化,那么就需要采用冷卻措施來降溫,以保證渦輪葉片能夠正常工作。常用的冷卻措施包括在渦輪葉片上噴涂熱障涂層,或者采用氣膜冷卻技術(shù)。熱障涂層通常能夠提供兩三百度的冷卻溫度,剩下的近四百度冷卻溫度就要靠氣膜冷卻技術(shù)了。
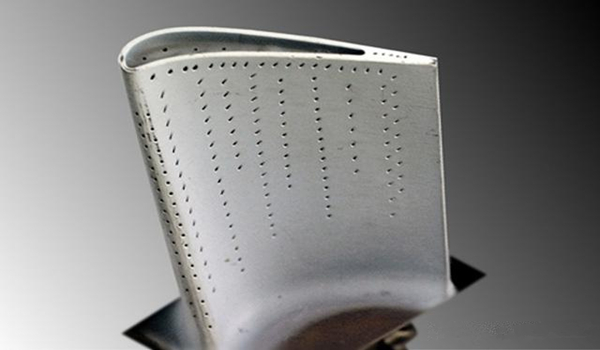
采用氣膜冷卻技術(shù)的渦輪葉片
我們先來說說氣膜冷卻,所謂氣膜冷卻就是在葉片表面打很多氣孔,在葉片內(nèi)部注入高壓冷卻空氣,經(jīng)氣孔排出,在葉片表面形成一層溫度較低的空氣膜將高溫的燃氣和渦輪葉片隔開。從上個世紀八十年代開始,發(fā)達國家就掌握了氣膜冷卻技術(shù),并且憑借這一先進技術(shù)確立起了航空發(fā)動機領域的領先地位。而我國航空發(fā)動機技術(shù)長期以來的技術(shù)落后跟沒有掌握先進的氣膜冷卻技術(shù)也有很大關(guān)系。
氣膜冷卻的渦輪葉片的內(nèi)部結(jié)構(gòu)
氣膜冷卻一般通過在渦輪葉片上打大量不同直徑的氣膜孔來實現(xiàn),孔徑約為100~700微米,且空間分布復雜,多為斜孔,角度為15°到90°不等。早期氣膜孔為簡單的圓形孔,為了提高冷卻效率,后發(fā)展為扇形或矩形等異形孔,現(xiàn)在已經(jīng)發(fā)展到復雜的異形孔如貓耳形孔。
這三種氣膜孔從上到下分別是圓形孔、扇形孔和貓耳形孔
因為氣膜孔直徑很小而且形狀復雜,無法靠鑄造直接成型,因此都是在鑄造完畢后另行加工的,這就給加工帶來極大的難度。目前主流的方法是電火花機床加工,但工具電極制造極為困難,很難加工小于200微米的孔,但是復雜異形孔往往需要50微米的加工精度而且要有三維精密加工能力,這對電火花加工來說很難實現(xiàn)。而且,渦輪葉片表面通常要覆蓋一層熱障涂層、一般是陶瓷材料,因為不導電,采用傳統(tǒng)電火花機床無法加工。只能先打孔再噴涂熱障涂層,然后再擴孔的方法。但是需要頻繁的檢測及二次擴孔。二次擴孔又面臨精確對準難題,而且會對孔周邊的涂層產(chǎn)生損傷,因此氣膜孔加工的質(zhì)量難以保證。隨著未來發(fā)動機渦輪葉片材料逐漸走向非金屬化,電火花加工更不靠譜。
隨后又發(fā)展了超聲-電火花加工,先用超聲穿透陶瓷涂層,再用電火花加工金屬部分。或者先用強激光打穿陶瓷涂層,再用弱激光加工金屬部分。這基本上都是復合加工,沿用的都是先涂層再打孔的思路,但是這樣工藝復雜,很不理想。對單晶葉片來說還有個難題要克服,那就是熱損傷,因此技術(shù)難度更大。
上個世紀六十年代又發(fā)展了電化學射流也就是電液束流加工技術(shù)來加工葉片,這一技術(shù)可以獲得無再鑄層、微裂紋、熱影響區(qū)表面,但加工效率很低。而且存在雜散腐蝕現(xiàn)象,導致開孔的輪廓形狀難以控制,因此也不是一種理想的氣膜孔加工手段。
要實現(xiàn)先進氣膜孔冷卻技術(shù),需要拋棄先開孔后涂層的加工工藝。要在一次裝卡過程完成全部加工,也就是要實現(xiàn)單步單機打孔。這樣就只能考慮用激光來加工,早期激光加工多采用毫秒級激光,但是這樣的長脈沖激光熱影響區(qū)嚴重,不適合單晶葉片。后來飛秒激光的出現(xiàn)才解決了問題。飛秒激光是一種以脈沖形式運轉(zhuǎn)的激光,持續(xù)時間非常短,屬于飛秒量級,1飛秒就是1/1000萬億秒。它的瞬時功率非常高,可達到百萬億瓦。能量來不及釋放該脈沖已經(jīng)結(jié)束,避免了能量的轉(zhuǎn)移、轉(zhuǎn)化熱量的存在和熱擴散,實現(xiàn)了真正意義上的激光“冷”加工。這樣加工時切面整齊、無熱擴散、無微裂紋及冶金缺陷,加工過程中不會對所涉及的空間范圍的周圍材料造成影響,從而做到了加工的超精細。
右邊這個是貓耳形氣膜孔的實際外形照片
2017年,中國科學院西安光學精密機械研究所,開發(fā)出國內(nèi)最高單脈沖能量的26瓦工業(yè)級飛秒光纖激光器,研制出系列化超快激光極端制造裝備。在國際上率先突破了小空腔0.5毫米葉片對壁無損傷微孔加工的世界技術(shù)難題,在國內(nèi)率先攻克了高精度、三維可編程、異型微結(jié)構(gòu)掃描成形技術(shù),實現(xiàn)了超高精度50±2微米及異型氣膜孔的高品質(zhì)加工,為實現(xiàn)先進氣膜冷卻技術(shù)提供了重要的技術(shù)支撐,達到了國際領先水平。完成了國產(chǎn)發(fā)動機多型號、多批次高壓渦輪單晶葉片的氣膜孔加工及驗證。
超高精度的氣膜孔
而且,這一技術(shù)也為我國發(fā)展渦輪葉片發(fā)散冷卻技術(shù)打下了良好基礎。發(fā)散冷卻又稱發(fā)汗冷卻,可以實現(xiàn)比氣膜冷卻更高的冷卻溫度。但實現(xiàn)技術(shù)難度也更大,因為發(fā)散冷卻需要在葉片表面開更多更小的氣孔,完全覆蓋葉片表面。而飛秒激光打孔就有這樣的潛力。雖然無法確定展臺上的渦輪葉片是否使用了飛秒激光打孔技術(shù),但我們確確實實掌握了這一先進技術(shù)。關(guān)于氣膜冷卻技術(shù)我們先說到這里,下次來我們來談談我國在熱障涂層技術(shù)上的創(chuàng)新。
轉(zhuǎn)載請注明出處。